
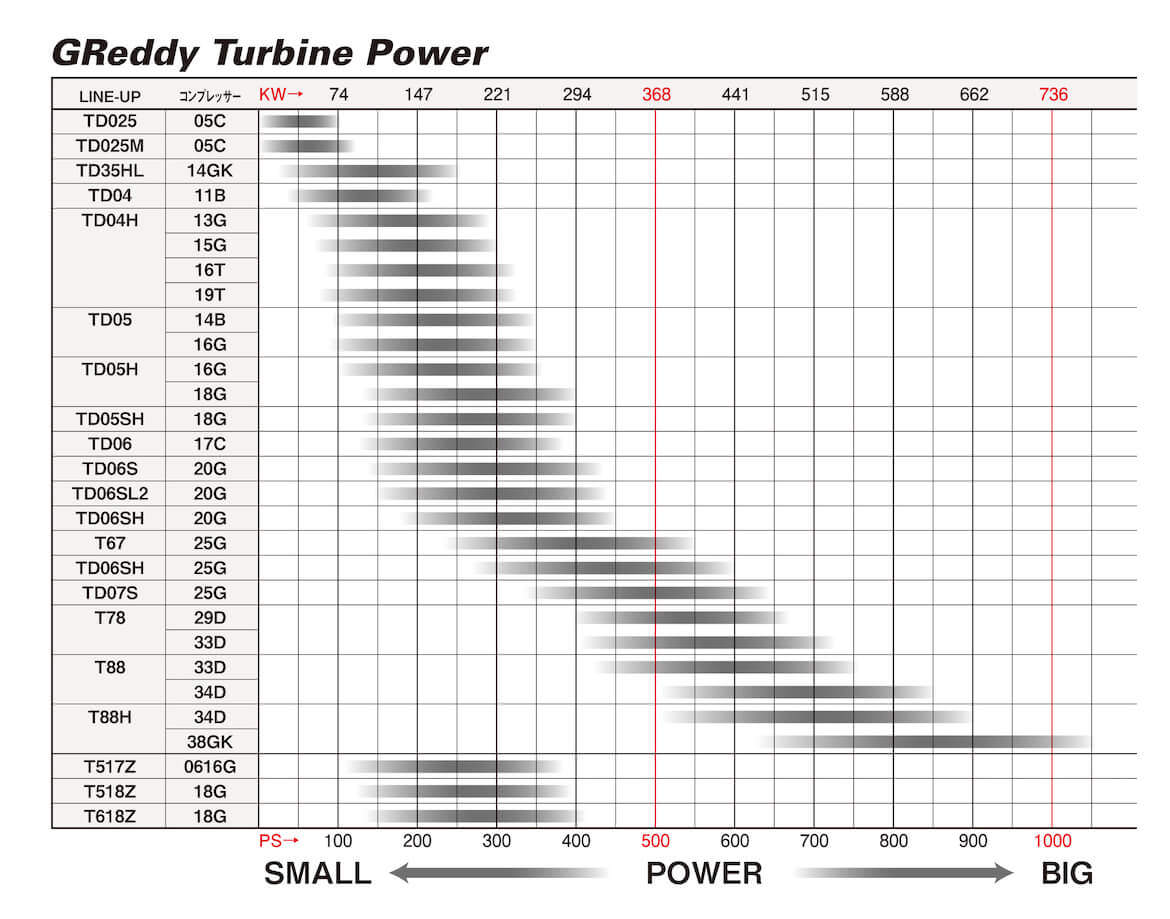
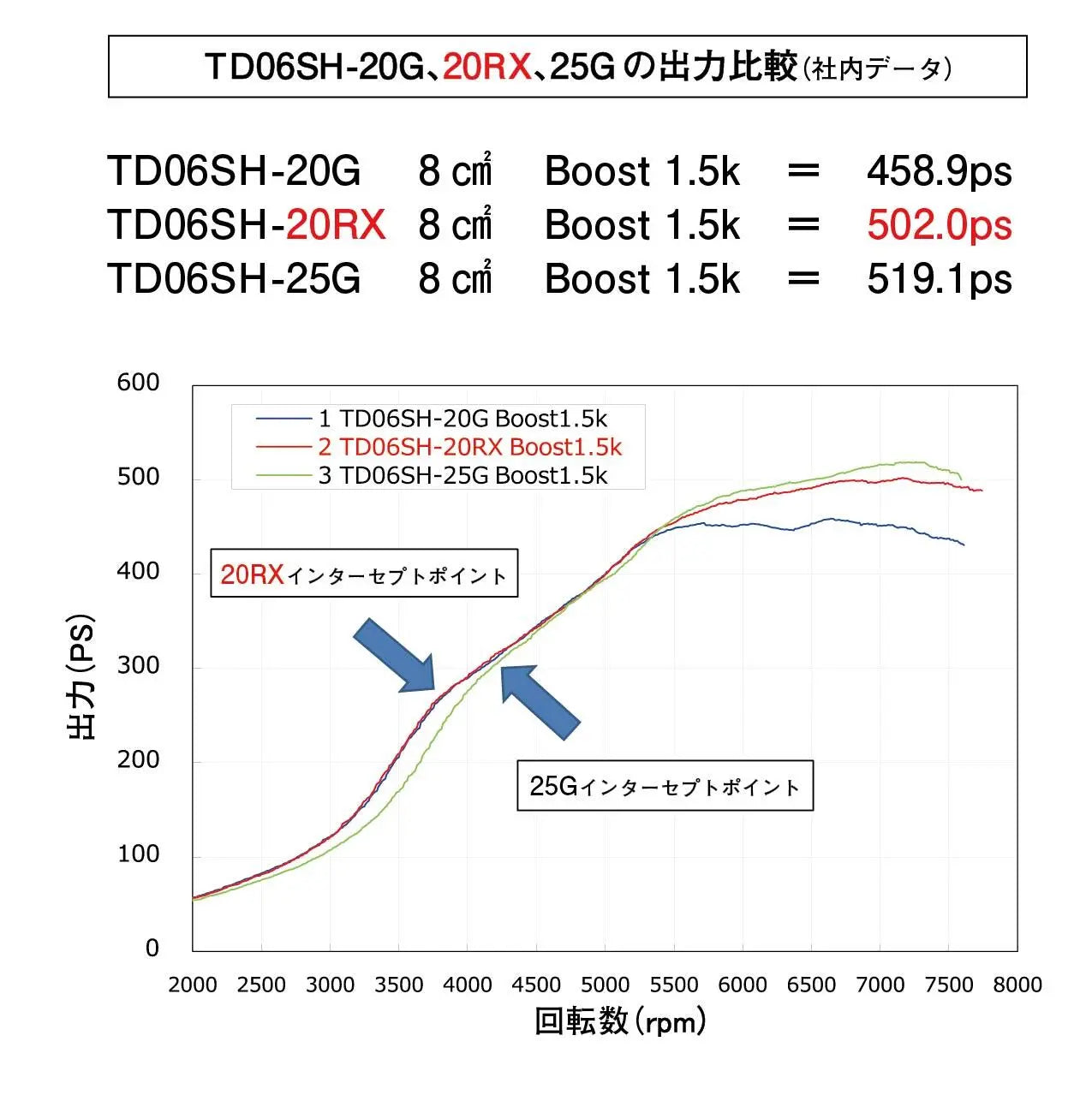
GREDDY TD06S L2 20RX TURBO EXT W/G - (11500340 11500341)
TD06S L2 20RX | 8.0 | external w/g | 11500340 |
TD06S L2 20RX | 10.0 | external w/g | 11500341 |
GReddy TD06S L2-20RX 8㎠ / 10㎠
Adopting a newly designed aluminum billet impeller, performance exceeds that of the TD06SH 20G
●The compressor wheel uses a newly designed aluminum billet impeller with excellent high-temperature strength.
●The aluminum billet impeller is machined from a high-strength aluminum alloy, making it possible to make it thinner. As a result, the blade area is increased, air volume is increased, and at the same time, the compressor wheel is made lighter, improving response.
●Compared to the previously used G-type impeller, output in the mid-to-high speed range has increased by 9 to 12%, while response in the low to medium speed range remains the same.
*Installation of a blow-off valve at the same time is recommended.
Specification
Features of GReddy Turbocharger mechanism and features:
Compressor and turbine housings and wheels designed for high efficiency, a turbocharger uses the "pressure" from the exhaust gas discharged from the engine to rotate a turbine wheel, and a compressor wheel mounted on the same shaft rotates together to provide supercharging. For this reason, if the turbine wheel is made smaller, the turbine will rotate at low speeds even with an engine with a small displacement, but if the turbine wheel is made large with a small displacement, the turbine will not rotate until high speeds, where the pressure of the exhaust gas increases. It will be. It can be said that the relationship between the "size and shape of the turbine wheel" and "exhaust gas pressure" influences engine characteristics. Also, once you understand the principle of a turbocharger, you may think, ``If I keep the turbine wheel small and make the compressor wheel large, I can get high boost pressure even with a small displacement engine.'' This is the "hybrid turbine" that Trust is best at. Considering the rotational balance of the turbine wheel and compressor wheel, we selected the most efficient size, shape, and number of wheels. Furthermore, the GReddy turbocharger is characterized by an ``ultra-high performance turbine that can obtain high output even with a small displacement'' created by combining a housing that matches these characteristics.
Advantages of a large floating journal bearing:
GReddy turbochargers are particular about floating journal bearing. This is because it is the bearing method that provides the least resistance during actual use. When you disassemble floating metal, it appears as if the metals are in contact with each other, so you tend to think of it as a metal with high frictional resistance. Also, when you turn the compressor wheel by hand when the turbocharger is cold, it will feel heavier than the ball bearing type. Still, why is floating metal superior? The answer is because of the presence of "engine oil." When the engine is started and oil pressure is applied and the engine oil becomes warm, the shaft will be covered in oil and floating in the center of the metal. This is a "hydrodynamic bearing system" that supports the shaft using only oil. Floating = Floating, which is why it is called metal. In other words, when disassembling metal, the most important component, the engine oil, is drained before work, so it is no exaggeration to say that the most important device is overlooked. During actual use, the space between the metal and the shaft is filled with oil, and the metals do not touch each other at all. In short, it would be easier to understand if you say that even if you rotate the compressor wheel when the turbocharger is cold and compare the weight of the rotation, you are comparing at a place where the performance of the floating metal is not achieved. The performance of a turbocharger when it is actually in use is important, and comparing performance when the engine is stopped has little meaning. When the temperature of the turbocharger reaches the point where it is actually used, which would have less resistance: a bearing system in which the metals are in contact with each other even though they are supported at points, or a fluid bearing system in which there is no metal contact at all? Fluid bearings also do not require circulation of cooling water like ball bearings, so you can see that there is no frictional heat generated around the metal.
As we pursue performance and convenience in the temperature range where turbochargers are actually used, we end up with floating metal fluid bearings.
